Application:
General Fabrication
Education
Processes:
Synergy Control
Pulse MIG
Double Pulse MIG
HSP (High Speed Pulse)
Input Voltage:
3PH ~ 400V ±15%
Amperage Range:10-360A
Duty Cycle(40℃) 60%:
360A / 32V(GMAW)
Weight: 56KG
Advanced Features
Synergy Control - Set weld procedures with one control. Just easily takes 3 Steps to achieve weld perfection.
Superior aluminum performance - The upgraded pulse MIG has higher peak current and larger energy reserve. The perfect waveform achieves the heat control for aluminum welding, and virtually eliminates burn-through and warping issues on thinner materials. With double pulse, no need to swing, get better weld quality and appearance.
Improved Operation Process & Controls - Initial Arc control, Burn Back control, Arc Length control, Dynamic control, these make an easier operation and handling for welding.
High Speed Pulse MIG (HSP) - Specifically designed for demanding workshop use, the deposition rate can increase 25~48 % for mild steels by comparing with MAG process.
Excellent Arc Performance - By the advanced wave control system, the PROMIG 360SYN DPulse optimized the maximum performance with the most common filler metals, wire diameters and gas mixtures, and very suitable for general fabrications and welding educations.
Simple Operation but More Compatible
Simple operation
3 Steps to achieve weld perfection
1. Select operation mode.
2. Select Job-list No.
3. Adjust welding current.
Always the perfect setting by the synergic function using the material thickness.
Synergy control with job-list
The Job-lists display is easily and intuitively controlled through its graphical user interface. We assembled the perfect welding curve in every Job-No. for highly efficient multi-process welding of carbon steels and aluminum alloys. Operation is easier than ever before.
Separated wire feeder & remote control, robotic ready (as optional)
Robotic with advanced MIG process package, achieve ultra-high efficient welding with perfect welding performance. Optional package for robot interface by Analog connectors or Digital ports including EtherNetlP, DeviceNet, CAN, CANOPEN, RJ485 etc.
Robot Welding Requirement |
Synergy Control | ● |
Pulse MIG | ● |
Double Pulse MIG | ● |
HSP |
● |
HSA |
○ |
ULS |
○ |
HSS |
○ |
HPC | ○ |
MDP |
○ |
● Standard options | ○ Optionally available |
Better Aluminum Welding Process
Pulse MIG with larger current difference
The PROMIG 360SYN DPulse is an upgraded module and machine that is compatible with more advanced pulse processes. The PROMIG 360SYN DPulse improves on the standard pulsing process to provide a higher peak current and a larger current difference that is more suitable for Aluminum alloy welding. As wire speed increases/decreases, the pulse or MIG parameters also increase/decrease to match the right amount of power needed to achieve a more perfect welding curve.
With optional Push-Pull gun, the outstanding aluminum welding performance can be achieved much faster and more easily.
Double Pulse MIG
The double pulse is a combination of the Pulse MIG process and the variation of the high and low currents, with the low pulse section providing cooling time to the melt pool while simulating the oscillation so that the melt pool oscillates. So no need to swing, You can easily get a cosmetically pleasing weld seam, with significantly lower and more controller heat input into the workpiece. It results in much lower distortion and less rework for Aluminum sheets.
HSS is the high speed spot welding, which is perfectly combining the welding process, arc physics, high dynamic power response and powerful motor control technology, short in arc ignition time and arc ending time, a welding spool can be formed swiftly. A spot welding cycle is quickly completed, cycle over and over, by adjusting the time gap with the robot to get the fish scale you wish, weld seam is clear and beautiful.
Advanced Technologies for Higher Efficiency
HSP - High Speed Pulse Technology
Specifically designed for demanding workshop use, the deposition rate can increase 25~48 % for various materials, whether used in manufacturing thick materials or sheet metal.
The High-Speed Pulse(HSP) process enables you to save time, money, and energy compared to traditional pulse welding. This process is ready to raise pulse welding to a whole new level!
In general, One pulse melt one droplet, but we increase the submission of these droplets by TOPWELL’s New High-Speed pulse process.The transition will be faster, narrower HAZ zone and deeper penetration!
Get better welding seam
Less heat input, less spatters, less rework.
Get higher welding strength
Deeper penetration, no undercut defects, higher strength.
HSA - High Speed Spray Arc
The perfect combination of a highly concentrated and extremely stable arc with high density. HSA delivers deeper penetration, narrower heating zone, allows smaller opening angles for multi-layer welding, significantly improves the welding speed up to 30% faster than conventional MIG-MAG welding. It makes welding more efficient and more economical.
Smaller opening angle
Deeper penetration
More material saving
Higher welding efficiency
ULS - Ultra Low Spatters
The ULS process is a modified short-arc transfer arc with perfect waveform setting that greatly reduces spatter generation. In the pinch phrase, there is a special current interruption, the energy is extracted under the program setting, avoiding the explosion caused by the large current, and the surface tension of the molten pool warms the generated droplets. Even in CO2 and MAG welding, it can minimize the spatters, which means less rework, fewer rejects, less cleaning required and savings on wearing parts.
HSS - High Speed Spot Technology
HSS is the high speed spot welding, which is perfectly combining the welding process, arc physics, high dynamic power response and powerful motor control technology, short in arc ignition time and arc ending time, a welding spool can be formed swiftly. A spot welding cycle is quickly completed, cycle over and over, by adjusting the time gap with the robot to get the fish scale you wish, weld seam is clear and beautiful.
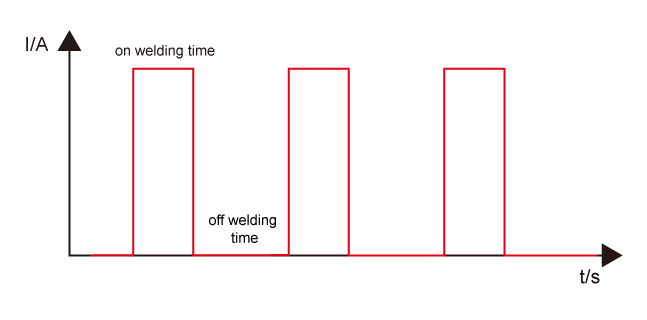
Tack welding: by robot
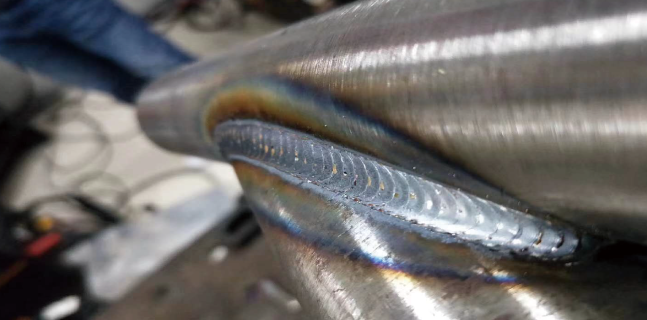
Widely applied on the thin (≤2mm thickness) pipes or frame/structure welding jobs.
HPC - Hybrid Pulse Control
The key is synergetic waveform controlled welding process control variants applied in MIG welding which are Pulse(spray arc) and short-circuit transfer types in one duty cycle. It delivers exceptional directional stability, deep penetration and free-spatters.
HPC Vertical-up Welding Process
The secret is the combination of two processes: one is the high energy phase to heat up the material quickly. Topwell's control technology ensures a perfect transition to the rapidly reduced energy phase. It ensures reliable penetration, precisely sized weld filling and a near- optimal throat thickness.Vertical-up welding with Topwell's HPC process is significantly much faster and simpler than classical "X-Mas tree".
MDP - Micro Double Process
MDP is Micro Double Process, ultra-precise on the synergy Pulse wave-form controlled process-control, freely adjust the weld seam chevrons from coarse to fine. The key is that when the high and low pulses alternate, there is no droplet formation in the low pulse phase. The advantage of MDP are precise energy input, low distortion, perfect TIG-like welding appearance easily produced by anyone, and the welding productivity can up to twice as quick as the conventional TIG. MDP is particularly suitable for thin to medium-walled (1-8mm) Aluminum, Steel, and CrNi applications, like frames, tables, beds, and furniture structures.
Improved Operation Process & Controls
Arc Length control
By changing the distance between torch and workpiece. You can now react much more easily to control the arc, such as changing gap dimensions or arc blow, more intuitively and with greater efficiency !
Dynamic control
Dynamic control allows the welder, for the first time, to variably adjust a pulse welding machine to a wide range of jobs and welding positions as well as to his personal preferences. The welder can use a controller to directly access the arc characteristic and change it from soft to hard.
Initial Arc control & Burn Back control
Initial Arc control is used to improve the success rate of arc ignition and form a smaller molten ball. Burn Back control enhances the function of eliminating molten ball, making the secondary arc initial easier.
LET'S STAY IN TOUCH
Get updates on sales specials and more
FOLLOW US
We want to hear from you!